What HR Should Know About Supply Chain Management: Processes, Systems, and Technology
February 10, 2025
Introduction
In today’s interwoven business environment, the success of an enterprise often depends on the seamless integration of its core functions. Supply Chain Management (SCM) and Human Capital Management (HCM) are two critical areas where collaboration can significantly enhance operational efficiency, productivity, and success. While SCM focuses on the movement of goods and services, HCM ensures that the right people are in place to drive these operations forward. In this article we explore the important components of SCM, its connections with HR processes, and how modern technology solutions enable organizations to manage SCM and HCM in a coordinated and efficient manner.
Understanding Supply Chain Management (SCM)
Definition and Scope
Definition of Supply Chain Management (SCM) for HR Professionals
Supply Chain Management (SCM) refers to the coordination, integration, and oversight of all activities involved in producing and delivering a product or service to customers. It encompasses the entire process from sourcing raw materials, manufacturing goods, and storing them, to managing inventory, distributing finished products, and providing post-sale services.
SCM aims to ensure that the right products or services are delivered to the right place, at the right time, in the most cost-effective and efficient manner. This requires collaboration across multiple stakeholders, including suppliers, manufacturers, distributors, and retailers, as well as robust systems for tracking and optimizing the flow of materials, information, and finances across the supply chain.
Modern SCM also focuses on risk management, sustainability, and resilience, particularly in an era of globalized trade and complex interdependencies. It relies heavily on technology, such as data analytics, automation, and AI, to improve decision-making, streamline operations, and adapt to disruptions.
From an HR perspective, SCM requires skilled talent across diverse roles, from logistics managers and procurement specialists to analysts and warehouse staff. HR plays a critical role in recruiting, training, and supporting the workforce that powers the supply chain, fostering collaboration, and driving innovations that align with organizational goals.
Key Components of Supply Chain Management
Supply Chain Planning – This is the initial stage where companies strategize how to manage all the resources that go into meeting customer demand for their product or service. Effective planning ensures that the supply chain operates efficiently and meets organizational goals.
Sourcing and Procurement – Identifying and selecting the suppliers that will provide the goods and services needed to create the product or deliver the service. Companies must establish processes to monitor and manage supplier relationships, ensuring that materials are of high quality and delivered on time.
Inventory Management – Comprises the managing of the inventory of raw materials, work-in-progress items, and finished goods. Effective inventory management ensures that companies have the right amount of stock to meet customer demand without overproducing and associated excess inventory costs.
Manufacturing – This component involves the actual production of goods. It includes activities such as assembling, testing, and packaging. Types of Manufacturing include Discrete Manufacturing, Process Manufacturing, and Contract Manufacturing. Efficient manufacturing processes are crucial for maintaining product quality and meeting customer demand.
Order Management – Involves the tracking, handling, and fulfillment of customer orders from inception to delivery. It encompasses every step in the order lifecycle, ensuring that products move efficiently from manufacturers to end customers. Typically, process steps include Order Creation, Order Processing, Order Fulfillment, Shipping and Delivery, and Returns Management.
Logistics – This involves the transportation and delivery of goods to various locations. Logistics ensures that products are delivered to the right place at the right time, optimizing routes and managing transportation costs. Warehouse Management is a key component of overall logistics, as well as inventory management and order fulfillment.
Maintenance – Maintenance consists of the regular, scheduled maintenance activities designed to prevent equipment failures before they occur. It includes tasks such as inspections, adjustments, cleaning, and parts replacement. The goal is to maintain equipment in good working condition and avoid unplanned downtime. Emergency and corrective maintenance also is included in the category.
Product Lifecycle Management (PLM) – Is the strategic approach to managing the entire lifecycle of a product, from its initial concept and design through production, distribution, and end-of-life disposal or recycling. PLM integrates people, processes, and technologies to ensure seamless collaboration and decision-making across all stages of the product lifecycle.
Key Goals of Supply Chain Management
Each organization approaches SCM with their own unique set of circumstances, requirements, and challenges. But in general, there are some common or shared goals of most SCM strategies. These include but are not limited to:
Cost Reduction – Minimizing costs associated with procurement, production, transportation, and inventory holding while maintaining or improving quality standards. Companies track cost savings through metrics such as cost per unit, total supply chain cost, and cost savings from process improvements.
Customer Service Enhancement – Ensuring high levels of customer satisfaction by delivering products and services in a timely manner, meeting customer expectations, and providing excellent post-sales support. Customer satisfaction can be measured using metrics like on-time delivery rate, order accuracy, customer feedback scores, and Net Promoter Score (NPS).
Inventory Optimization – Balancing inventory levels to meet demand while minimizing excess inventory and carrying costs. This involves implementing strategies such as just-in-time inventory management and demand forecasting. Key metrics include inventory turnover ratio, days of inventory on hand, and stockout rates.
Quality Improvement – Ensuring that products and services meet or exceed quality standards throughout the supply chain, from raw material sourcing to final delivery. Quality can be assessed using metrics such as defect rates, return rates, and customer complaints.
Flexibility and Agility – Building a supply chain that can quickly adapt to changes in demand, market conditions, and business requirements, enabling the organization to respond effectively to disruptions and opportunities. Flexibility and agility can be measured through metrics like response time to market changes, adaptability to new product introductions, and supply chain resilience.
The Connections Between Supply Chain Management (SCM) and Human Capital Management (HCM)
Shared Objectives
The intersection of Supply Chain Management (SCM) and Human Capital Management (HCM) revolves around optimizing resources—both physical and human—to ensure smooth and efficient operations. SCM and HCM share common goals of efficiency and resource optimization. Ensuring that the right talent is deployed in supply chain operations is essential to achieving business objectives. For example, a warehouse’s productivity depends on having sufficient staff to manage inventory and shipments.
Key areas of overlap and collaboration include:
Workforce Planning – Effective workforce planning is critical for managing supply chain operations. Ensuring the right number of employees with the right skills is available at each stage of the supply chain (e.g., production, logistics, and warehousing) is essential. SCM and HCM teams must work together to forecast demand and align workforce availability with peak periods and operational needs.
Talent Acquisition and Development – SCM often requires employees with specialized skills (e.g., logistics, procurement, data analysis). Recruiting and developing employees for these sometimes hard-to-fill roles ensures the supply chain functions efficiently. Joint initiatives between SCM and HCM teams to identify skills gaps and create training or development programs tailored to supply chain needs.
Employee Safety and Wellbeing – Ensuring the health and safety of employees in warehouses, manufacturing plants, and distribution centers is crucial for uninterrupted supply chain operations. HCM can implement safety training and compliance programs, while SCM can identify risks and operational safety needs.
Contingency Planning and Crisis Management – Disruptions in the supply chain (e.g., natural disasters, pandemics) require coordinated responses that include workforce redeployment or additional hiring. Having a flexible, resilient workforce in place can protect employers who may be forced to pivot rapidly.
Productivity and Performance Management – Measuring and improving workforce productivity directly impacts supply chain efficiency (e.g., order fulfillment rates, production output). HCM teams can design performance metrics, while SCM monitors how workforce performance impacts key supply chain KPIs.
Compliance and Regulatory Requirements – Supply chain operations often span multiple geographies with diverse labor laws and regulations. HCM ensures compliance with labor laws, while SCM monitors supplier and vendor adherence to regulatory standards.
Supporting Workforce Flexibility – Seasonal or project-based fluctuations in supply chain demand require flexible workforce models (e.g., contingent workers, gig economy). SCM and HCM need to align to recruit, onboard, and manage temporary or contract workers.
Technology Considerations for HCM and SCM Leaders
For most organizations, the proliferation of multiple enterprise systems can lead to increased complexity, higher costs, lengthy and expensive integration projects, inconsistent user experience, and higher administrative burdens of working with numerous technology providers. At H3 HR Advisors, we have consistently recommended that end user organizations seek to simplify their enterprise technology environments, often by consolidating functions with a platform provider of Enterprise Resources Planning (ERP) capabilities. Particularly for organizations involved in manufacturing, logistics, and resource intensive industries, the integration between SCM and HCM processes that modern ERP systems can provide is essential.
Modern ERP systems integrate Supply Chain Management (SCM) and Human Capital Management (HCM) functions to ensure seamless collaboration across both domains. Below are some specific examples of the functions, processes, data types, fields, and values that are shared and used between SCM and HCM, highlighting the key interdependencies in an ERP system:
Workforce Planning and Demand Forecasting:
Workforce planning (HCM) aligns with production schedules and seasonal demand forecasts (SCM). HCM employs predictive analysis to plan for future labor requirements based on supply chain demand.
Shared Data Types, Fields, and Values:
Employee availability: Fields like shift schedules, contract type, overtime limits.
Demand forecast data: Fields for production volumes, shipment schedules, and peak periods.
Skill requirements: Roles or job codes required for specific tasks in SCM (e.g., forklift operator, quality inspector).
Job Costing and Labor Allocation:
HCM tracks employee time and effort spent on supply chain tasks. SCM calculates labor costs as part of product costing and operational expenses.
Shared Data Types, Fields, and Values:
Time tracking data: Hours worked by employees linked to specific SCM activities or cost centers.
Cost codes: Job categories, department IDs, or work order numbers linked to labor.
Employee rates: Fields for hourly wages, overtime pay, or contractor fees.
Recruitment and Onboarding for Supply Chain Roles
SCM identifies workforce gaps for specific supply chain processes. HCM recruits, hires, and onboards employees to fill these gaps.
Shared Data Types, Fields, and Values:
Job requisitions: Fields for role title, required certifications, and location.
Onboarding workflows: Training modules, safety certifications, and equipment assignments for SCM roles.
Employee profiles: Fields for skills, certifications (e.g., forklift license), and availability.
Training and Compliance Management
HCM delivers training programs for safety, regulatory compliance, and technical skills required in SCM. SCM monitors compliance with industry standards and legal requirements.
Shared Data Types, Fields, and Values:
Training records: Completion dates, certifications earned, expiration dates.
Compliance data: OSHA, ISO certifications, and audit logs.
Risk assessments: Safety incidents or near-miss reports linked to employee profiles.
Time and Attendance for Shift Scheduling
HCM manages time-off requests, shift preferences, and attendance. SCM uses attendance data to plan shift coverage and production capacity.
Shared Data Types, Fields, and Values:
Shift schedules: Fields for employee ID, shift start/end times, and department.
Attendance records: Absences, late arrivals, and overtime logs.
Capacity data: Real-time availability of workers for specific shifts or tasks.
Payroll and Labor Cost Analysis
HCM processes payroll based on hours worked in supply chain roles. SCM analyzes labor costs as part of total operational expenses.
Shared Data Types, Fields, and Values:
Pay components: Overtime, shift differentials, and bonuses tied to SCM KPIs.
Cost allocations: Fields linking payroll to specific supply chain projects or departments.
Budget data: Approved labor budgets for SCM functions.
Asset Management and Maintenance
SCM tracks equipment maintenance schedules and downtime. HCM assigns trained employees to maintenance tasks or audits.
Shared Data Types, Fields, and Values:
Equipment data: Fields for asset ID, maintenance schedule, and assigned employees.
Certification data: Employees qualified to perform specific maintenance tasks.
Downtime tracking: Logs of maintenance activities and workforce involvement.
Employee Performance and Productivity Monitoring
HCM evaluates employee performance metrics. SCM analyzes workforce productivity in operational terms (e.g., units produced per hour).
Shared Data Types, Fields, and Values:
Performance metrics: Productivity rates, quality checks passed, and task completion times.
SCM KPIs: On-time delivery rates, order accuracy, and production throughput.
Incentive programs: Links between performance and bonuses or rewards.
Contingent Workforce and Vendor Management
HCM manages contracts and payments for contingent workers. SCM coordinates with vendors supplying temporary labor during peak demand.
Shared Data Types, Fields, and Values:
Vendor data: Contracts, SLAs, and payment terms for labor suppliers.
Contingent worker profiles: Fields for job roles, project assignments, and tenure.
Cost tracking: Expenses for temporary labor linked to SCM budgets.
Integration of Analytics and Reporting
Real-time dashboards integrate workforce (HCM) and supply chain (SCM) metrics for decision-making. Predictive analytics identify trends in workforce and supply chain efficiency.
Shared Data Types, Fields, and Values:
KPI dashboards: Metrics like turnover rates, workforce productivity, and order fulfillment.
Forecasting models: Data on workforce availability and supply chain demand.
Cost-benefit analysis: Links between workforce investments and supply chain outcomes.
Technology Strategies
While some organizations opt for Best of Breed approaches to their enterprise technology strategy, where they may have different, (and potentially multiple) systems from different providers for their SCM and HCM solutions, this strategy can lead to downstream challenges and problems. Primarily this approach establishes what can be significant integration complexity. Connecting separate platforms can be challenging, requiring middleware or custom APIs to ensure data synchronization. Integration issues could lead to delays, inefficiencies, or data silos. More technology providers also typically leads to higher overall technology costs for the organization. Separate licensing, support contracts, and integration efforts can increase overall costs. Additionally, maintaining integrations and resolving compatibility issues may require significant internal and external IT resources. Lastly, more enterprise systems leads to more inconsistent user experience across the organization’s enterprise technology environment. Employees may need to learn and use different interfaces and workflows, leading to inefficiencies and frustration.
Again, we generally recommend that organizations seek to reduce the number of disparate technologies in operation and to consolidate functions on ERP-type platforms where ever possible. A single platform ensures smooth data sharing and process workflows between SCM and HCM functions, eliminating integration complexity and lowers risk and overall costs. For example, Oracle Cloud Applications provides natively integrated modules across SCM and HCM that allow organizations to benefit from delivered integrations, data security and reliability, and supported upgrade paths. An integrated enterprise technology approach usually is more cost effective for the organization. Bundled solutions often reduce licensing, maintenance, and support costs, leading to more simplified IT infrastructure and fewer integration needs.
Additional benefits from technology consolidation with a provider like Oracle include a consistent user experience across the technology stack which leads to improved productivity and reduce training requirements. Unified platforms also provide the ability to produce better and faster information for decision-making. Native analytics tools embedded into the platform can easily combine data sources from SCM and HCM without complex integration or expensive custom development. A single data source enables unified reporting and analytics, supporting a more informed organization. Finally, with only one major technology supplier, the organization should benefit from heightened provider accountability. With one supplier, there’s a single point of accountability for support, updates, and resolving issues.
Conclusion
SCM and HCM are increasingly interconnected in modern enterprises. By leveraging technology and fostering collaboration between these functions, organizations can achieve operational excellence, improve employee satisfaction, and enhance customer experiences. As technology evolves, HR and supply chain leaders must work together to adopt systems and strategies that drive integration and innovation, ensuring long-term success in a competitive global market.
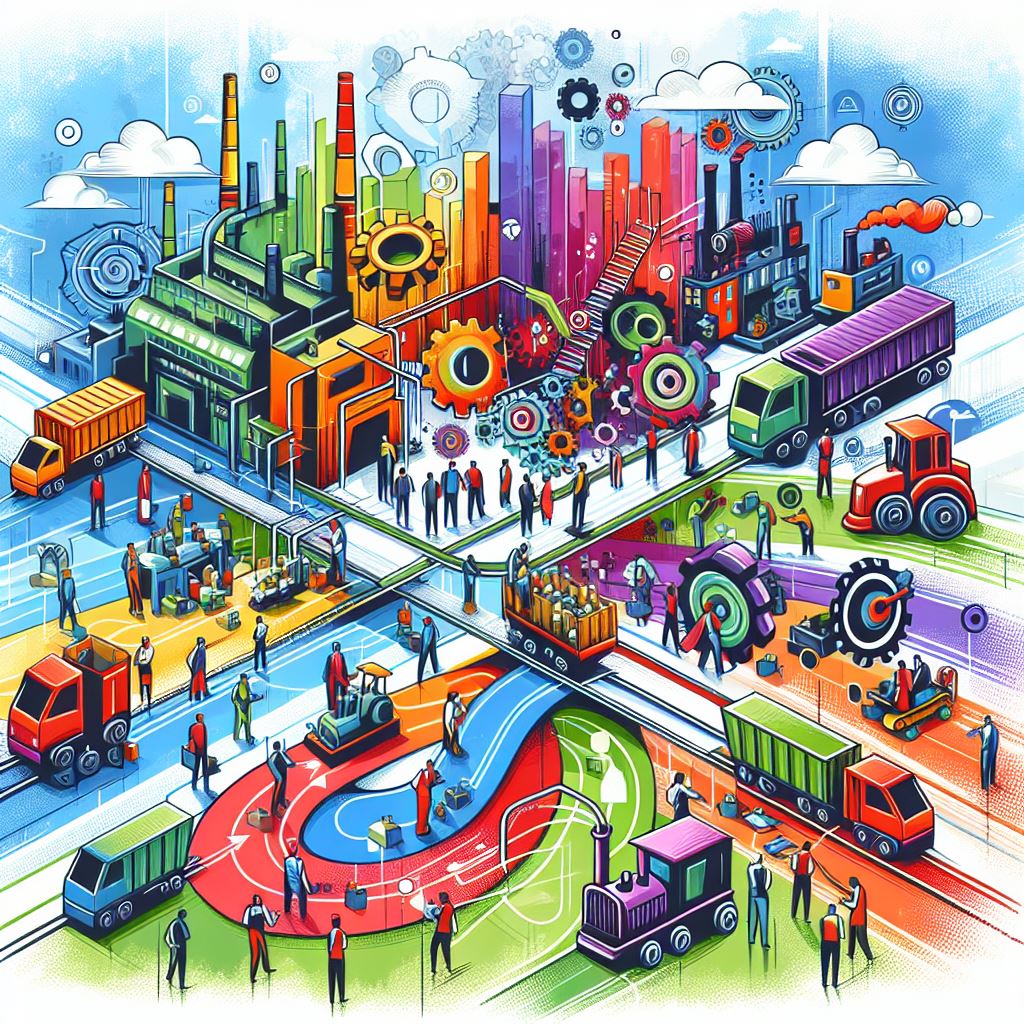
Author
Categories
Tags
Share
How we can help
Led by Trish Steed and Steve Boese, H3 HR Advisors harnesses over 40 years of experience to delivery HCM insights and guidance to global organizations.
H3 HR Advisory services
By leveraging technology, analytics, and our deep industry knowledge we can help you to reposition your workforce and ensure that you have the right people with the right capabilities in the right roles to positively impact the growth of your business.
HR Happy Hour Podcast Network
Created in 2009, The HR Happy Hour Show is hosted by Steve Boese and Trish Steed and is the longest continuously running internet radio show and podcast on Human Resources, HR Technology, Talent Practices, Workplace and Leadership topics.
H3 HR Speaking Services
We work closely with every client to customize your content - keynotes, webinars, research, infographics, and buyer’s guides - to inspire, educate and inform the audience enabling you to reset and realign your organization for a talent-led breakthrough.
Get in touch
Talk to us today and find out how we can help you and your organization leverage HCM technology to attract, onboard, retain and manage top talent.